Continuing the Aug 2018 Tip of the Month (TOTM) 1 on design and operation of unconventional surface facilities, this TOTM presents process safety tips for four case – studies:
- Direct Fired Heater Treater Burn Through Failures
- Tank Blanket Gas / Flame Arrestors
- Pocketing Vent / Relief Piping
- Hot Oiling of Oil Storage Tanks to meet TVP / RVP
We start this tip with a quote from a colleague, James A Britch: “I never regretted buying quality.” There is a lesson in there for unconventional batteries. There is tremendous pressure to reduce capital costs, but you should be focused on life cycle cost.
If you install equipment, and then burn down the battery…you haven’t saved much.
There’s the loss of capital, and loss of revenue from shut-in production.
PROCESS SAFETY CASE STUDY 1: DIRECT FIRED HEATER TREATER BURN THROUGH FAILURES
Direct fired burners are failing due to internal flame impingement directly on the steel, and salt build up on the outside of the firetube in the process fluids. The salts build up, act as an insulator, and then steel temperature increases until a burn through occurs. Since the process side of the burner operates at a higher pressure than the natural draft burner, the process fluids enter the burner, and ignite. In many instances this has resulted in massive damage to the entire battery.
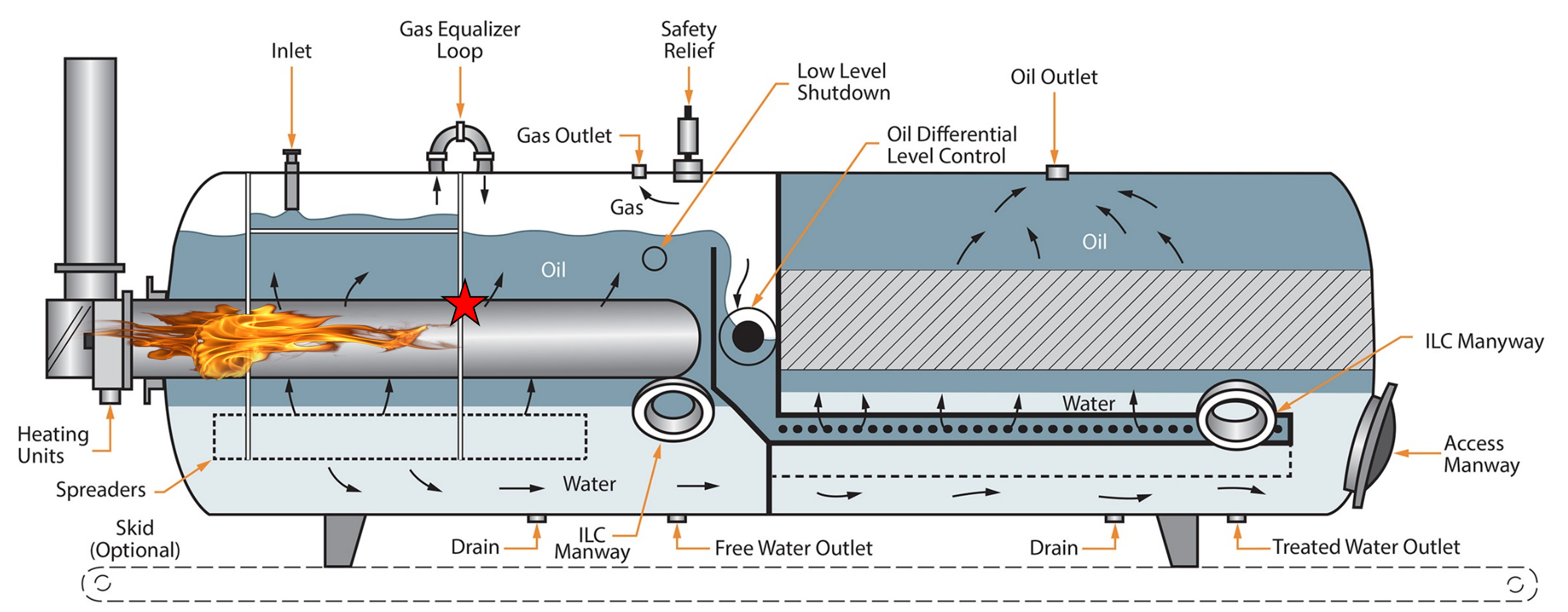
Figure 1 – Heater Treater Firetube Failure
Figure 1 illustrates the location of burn through failure that occurs in the 12 o’clock portion of the burner firetube (combustion leg).
Solutions to this issue are to use:
- Indirect fired heater where the process fluid flows through coils in a larger shell surrounded by a heat transfer fluid. The firetube burner is immersed in the heat transfer fluid within the same shell.
- This solves the salt build up failure mode, but not the flame impingement failure.
- Some operators use glycol as a heat transfer fluid. This is a cheaper alternative to expensive heat transfer fluids, but glycols degrade to acetic acid if the skin temperatures of the fire tubes exceed 350°F (177°C). These same operators rarely check the pH of their heat transfer fluid until leaks and severe corrosion are found. Heat transfer oils are a better choice.
- Direct fired heater with a ceramic sleeve to take the higher temperature shock of direct flame impingement. Heaters normally have ceramic refractory castables and bricks to prevent direct flame impingement. As shown in Figures 2 and 3 Bartz et al. 2 recommends inserting a ceramic tube to spread the heat flux of the flame and avoid burn through.
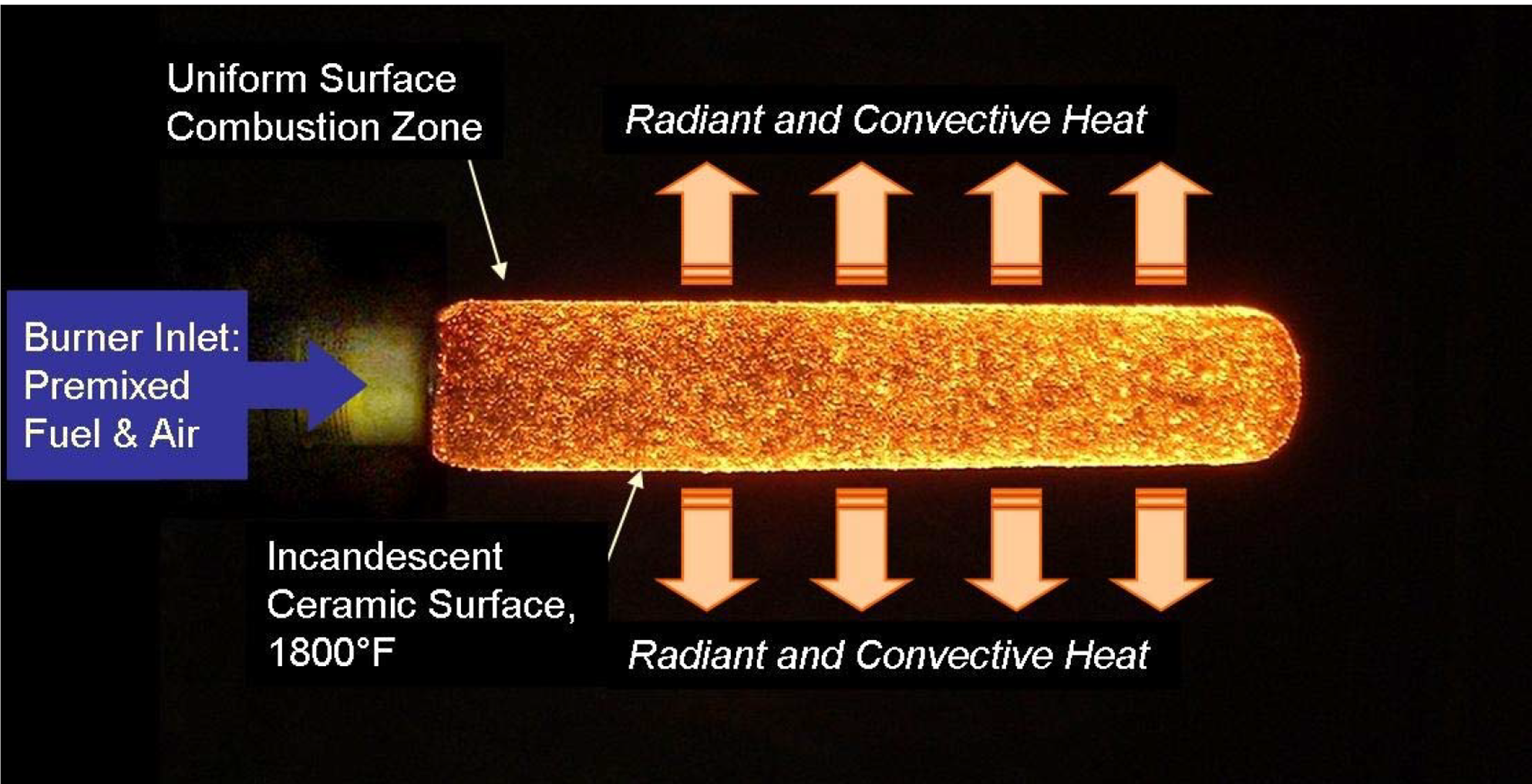
Figure 2 – ALZETA distributed flux burner 2
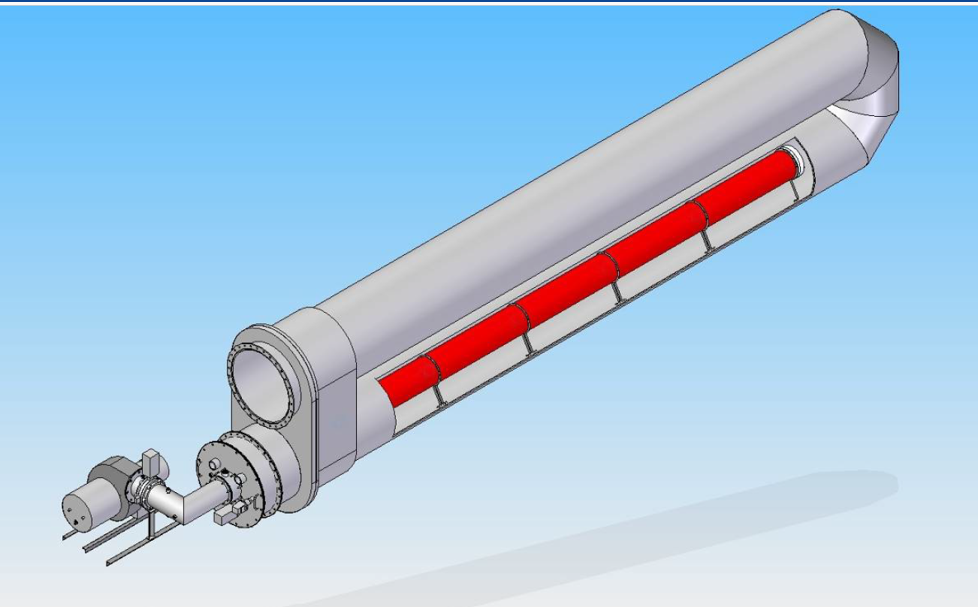
Figure 3 – ALZETA general arrangement of distributed flux burner and blower 2
- Best Solution: consider a separate furnace and heat exchanger using heat transfer oils. This solves both issues. The heat transfer oils are designed to operate without degradation at process temperatures required, and the metal temperatures in the heat exchanger will not cause metal failure if there are no salt deposits on the heat exchanger. This may require periodic hydro-blasting, but you will not have to rebuild the battery.
- Think Reliability has a free excellent Root Cause Analysis tool in Excel (Figure 4)
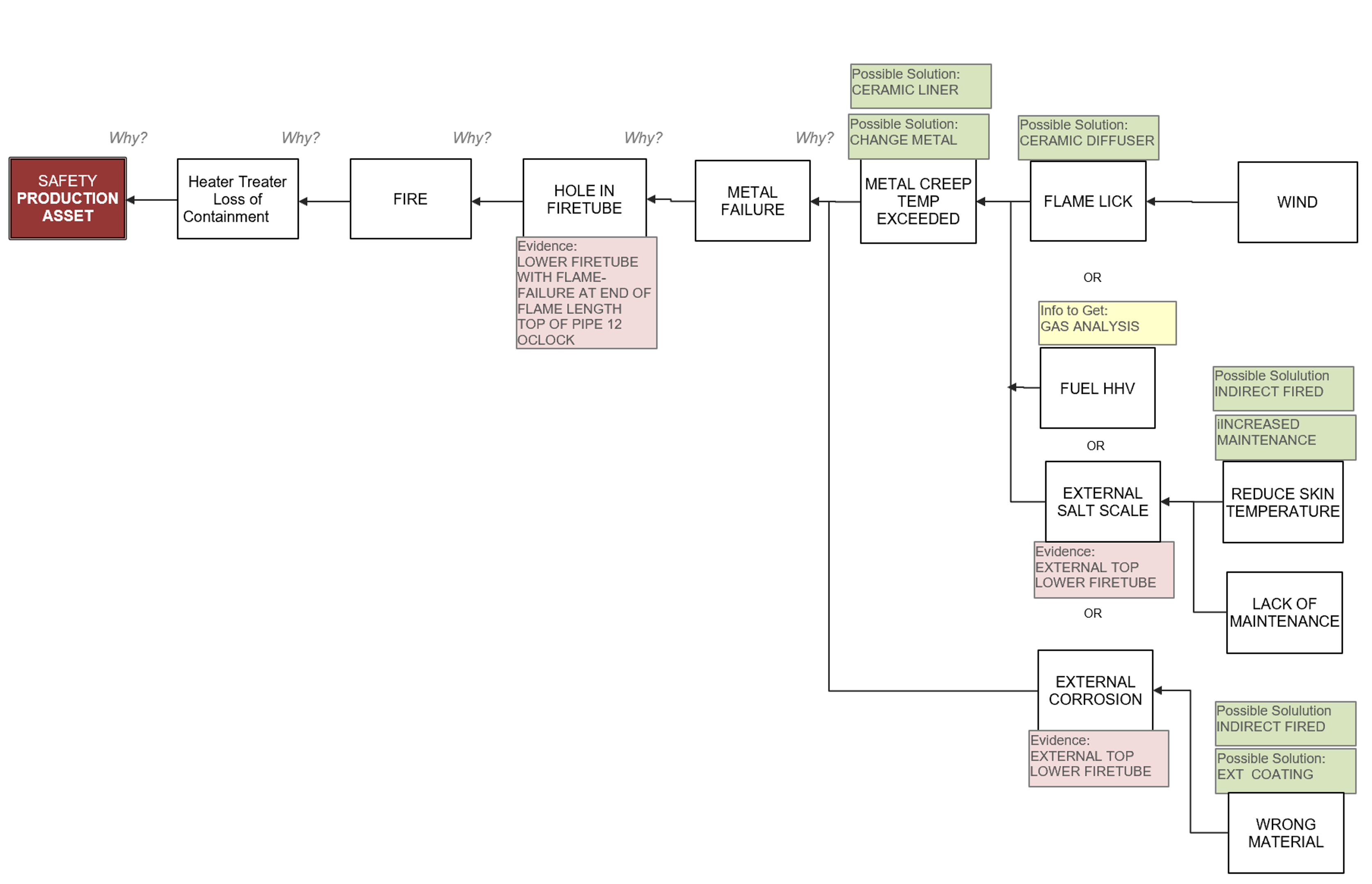
Figure 4 – CAUSE MAP for Burner Firetube Failures in Heater Treaters
PROCESS SAFETY CASE STUDY 2: TANK BLANKET GAS / FLAME ARRESTORS 3
Flame arrestors and tank blanket gas provide independent layers of protection between the ignition source – flare or thermal oxidizer – and the vapor space in the water and oil tanks. When evaluating what to use in a design consider using a layer of protection analysis or LOPA 3. This tool is discussed in the PetroSkills | John M Campbell PS4 – Process Safety Course. It provides a semi-quantitative solution to design decisions that are based of failure frequencies and not just personal preferences or gut feels. The more independent layers of protection the lower the frequency of the consequence occurring.
f= (IEF) x PFD1 x PFD2….
Where:
f = Frequency of the consequence occurring for the scenario
IEF = Frequency of the initiating event
PFD = Probability of the failure on demand for an independent layer of protection. For example, the probability that a relief valve will not operate as intended.
Flame arrestors have a Probability of Failure on Demand (PFD) with a range of 1×10-1 for arrestors without temperature indicators and an effective isolation / shutdown system, and tank blanket gas (BPCS-Basic Process Control System) has a PFD of 1×10-1 [3]. The designer can use both or either to provide independent layers of safety protection. Flame arrestors are subject to plugging from ice, corrosion, fouling, improper or lack of maintenance. Blanket gas works well in this situation due to the narrow range of flammability of methane in air (5-15% fuel to air). Majority of stock tank incidents occur during maintenance activities with small amounts of gas and large volumes of air.
During the high volume of production timeframe for unconventional tank batteries the stock tanks degas and have “auto-blanketing” of the active tank vapor space. But what happens in the future when rates are very low? What happens in water tanks that are not provided with gas blanketing? This also explains why water production tanks / injection batteries experience tank fires/explosions. In general, methane has a very low solubility in water – approximately 2 SCF/STB (0.36 Sm3/STm3) of water going from 250 psi (1724 kPa) to atmospheric pressure. This small volume often results in flammable mixtures in the vapor space of the tank.
It is a good practice to select tank blanketing as your first line of defense to prevent internal tank corrosion and gas plant amines and TEG process corrosion/solution degradation by keeping oxygen out of the system, and internal explosions from flash back from flares and thermal oxidizers.
PROCESS SAFETY CASE STUDY 3: POCKETING VENT / RELIEF PIPING
Many unconventional tank batteries run their vent / flare / thermal oxidizer piping at grade on sleepers with zero slope, and then jump vertically into a flare knockout (see Figure 5). This pocketed piping is a liquid trap for water and heavier hydrocarbons. Once a liquid pocket forms, the tanks overpressure, and then vent locally through their pressure/vacuum reliefs and thief hatches. In the winter this pocket can freeze and block the flare (see Figure 6). This can also cause a loss of containment when a PSV activates and cannot depressure to the flare. This causes a loss of revenue, as well as an environmental and safety issue. These vapors are extremely rich and normally are much heavier than air. This creates the potential for an unconfined vapor cloud explosion or flash fire locally.
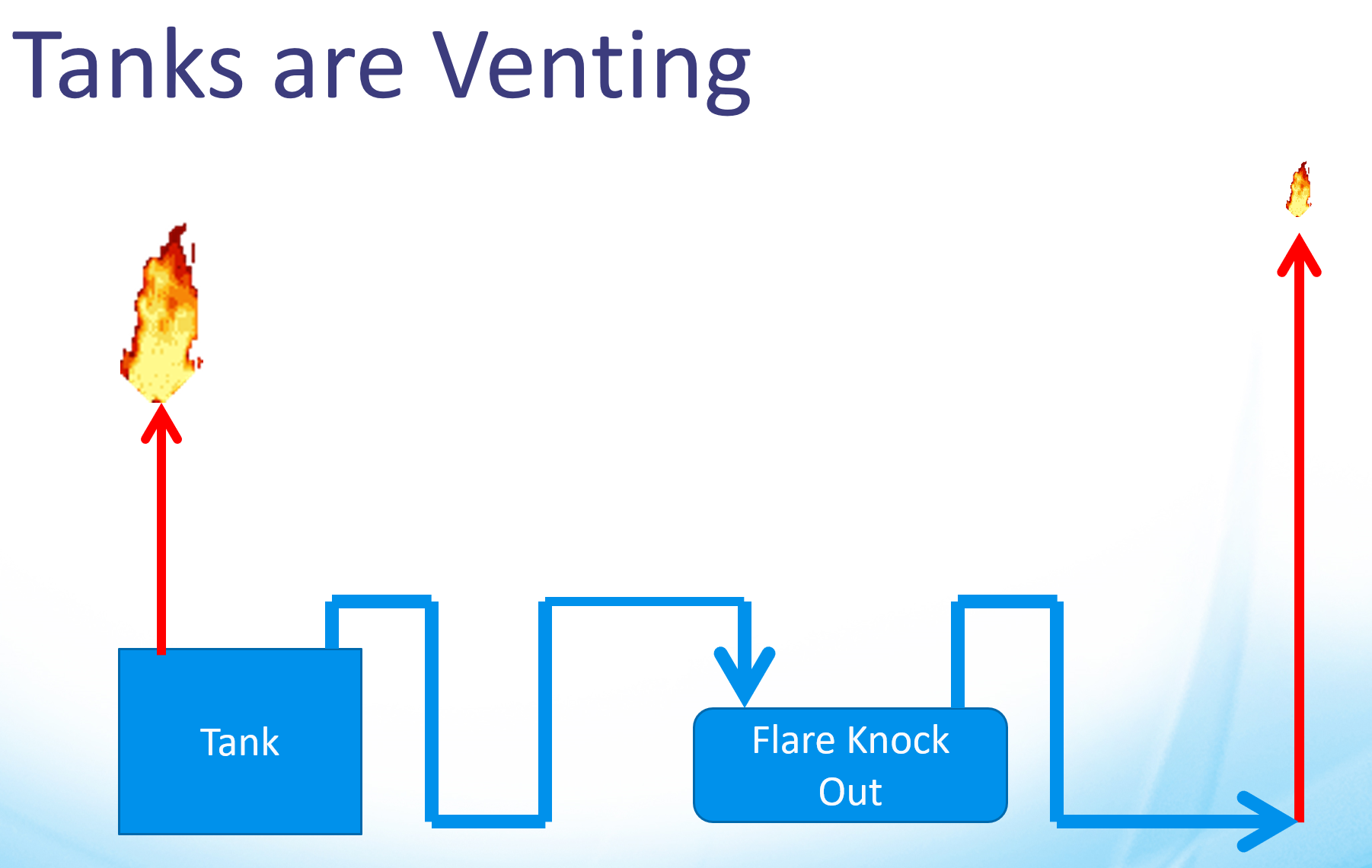
Figure 5 – Pocketed piping causes an overpressure in the tanks and results in venting
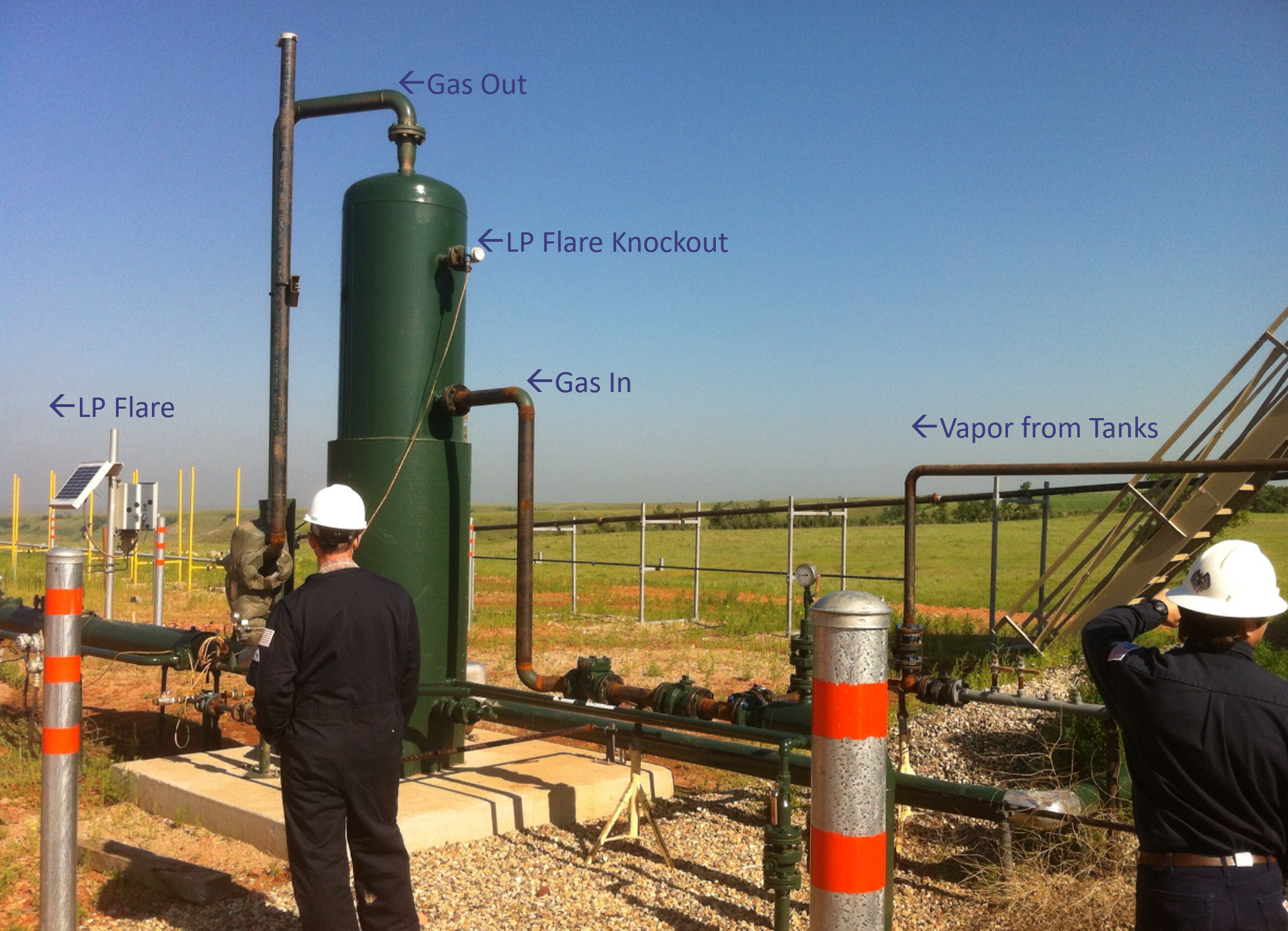
Figure 6 – This flare knock out has a 5 ft (1.5 m) pocket – tanks vent, and the potential for ice blockage in the winter
As illustrated in Figure 7, slope your vent/relief piping toward a lower elevation knock out or burn pit.
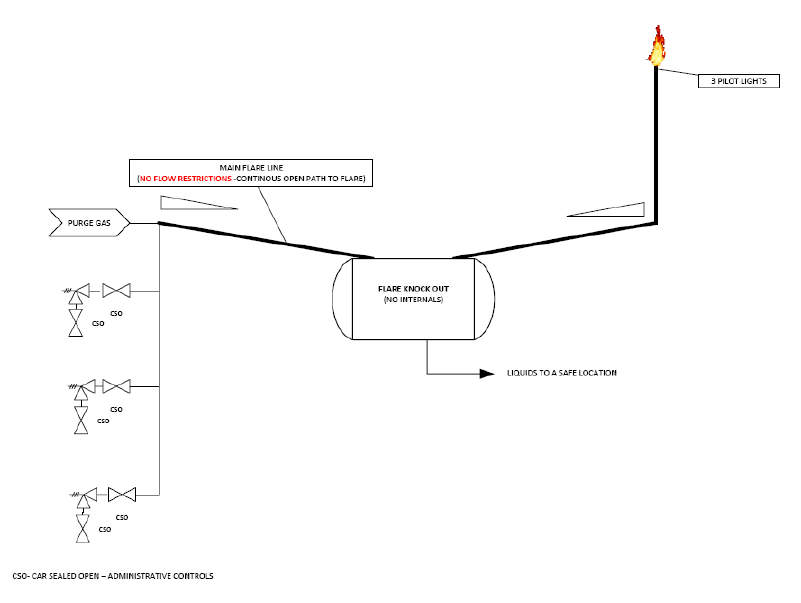
Figure 7 – Flare header design into knock out – sloped / no pockets
API Standard 521 4, pressure-relieving and depressuring systems, requires that the flare piping be free draining to the flare knock out drum, and then free draining from the flare back to the flare knock out.
These issues causing tanks to vent heavier than air molecules (propane/butane) can lead to flash fires and unconfined vapor cloud explosions (UCVE). Heavy vapor generally finds an ignition source. Figure 8 shows how oxygen may get into the oil stock tanks. Getting oxygen into your system causes major damage to the gas plant amine systems, and TEG systems, as well as general corrosion in your facilities.
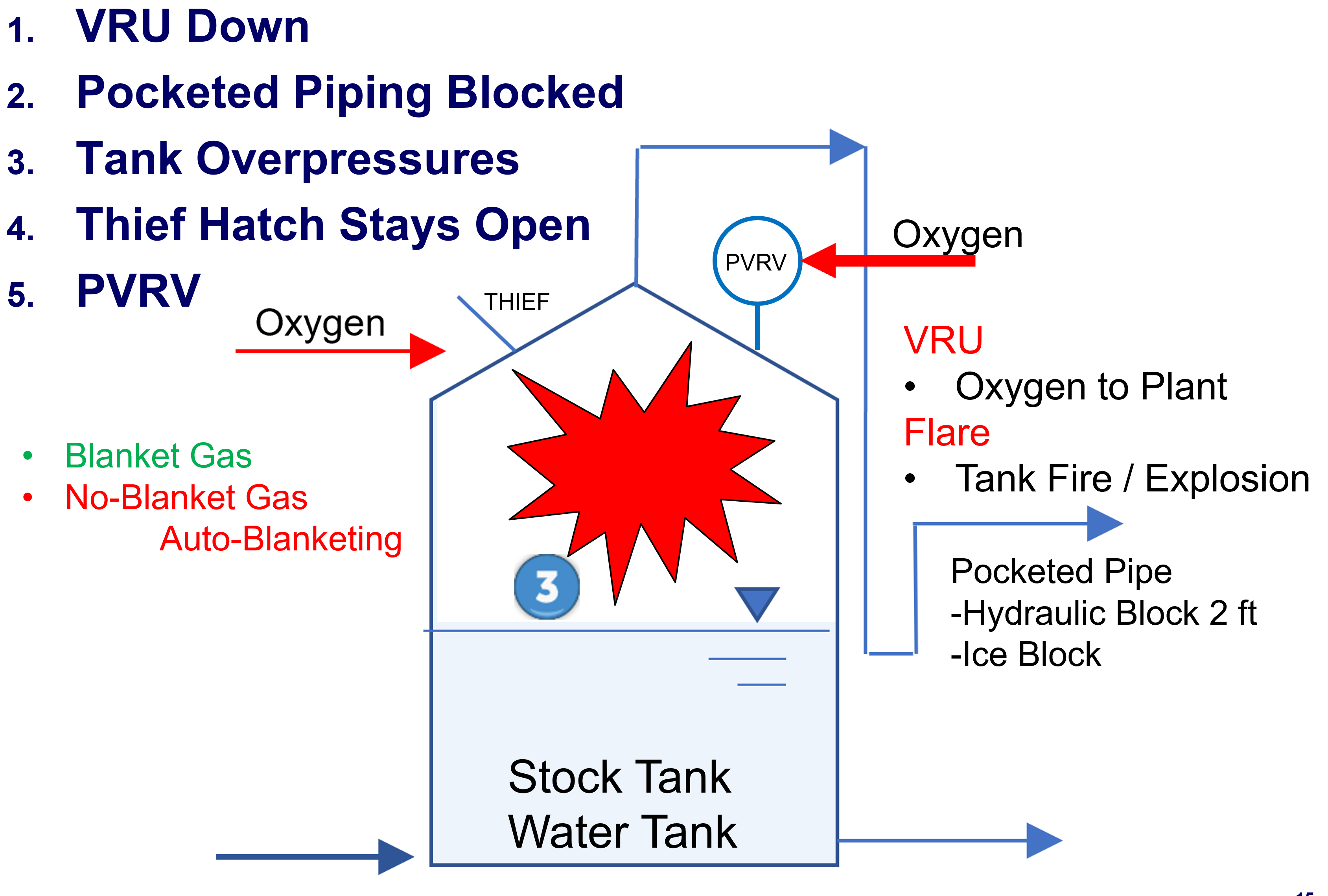
Figure 8 – How oxygen gets into your oil stock tanks & also causes venting
PROCESS SAFETY CASE STUDY 4: HOT OILING OIL STORAGE TANKS
As illustrated in Figure 9, some operators use hot oil trucks during winter months to heat the crude oil in the tanks to flash light ends off the crude to meet vapor pressure specifications for crude sales. The solution to this issue is not to use hot oil trucks but is to stabilize the crude or use a design using Vapor Recovery Towers (VRT) as discussed in the August 2018 Tip of the Month- Design and Operation of Unconventional Surface Facilities Issues-Stabilization 1.
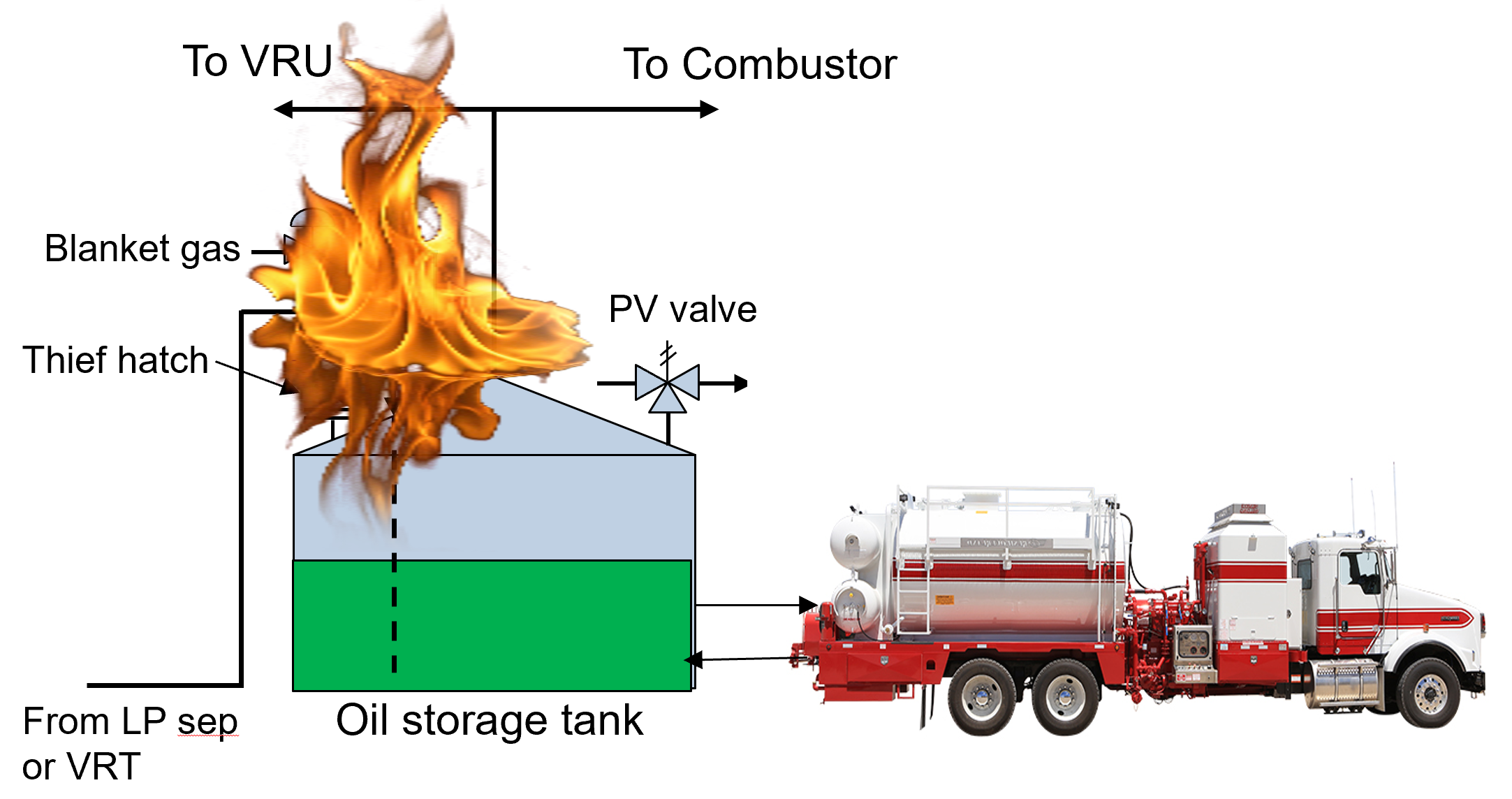
Figure 9 – Winter “Hot Oiling” of oil stock tanks
Many operators are faced with large numbers of tank batteries in the hundreds or thousands spread over a large geographic area. Many rely on unsupervised contractors to conduct hot oiling operations, oil & water loading and unloading, and other maintenance operations.
- Do you have an operator present at the location to help with hot oiling?
- Does the lease operator visit the site with the contractor to issue a Hot Work Permit and JSA?
- Do you have operating guidelines or checklists for Hot Oil Operations?
- Do they include monitoring of weather conditions? Wind Speed?
- Shutdown for low or no wind conditions?
- Do they include stopping of other operations such as oil / water truck loading?
- Are parts of the lease blocked off to prevent other vehicles entering as ignition sources?
- Are the hot oil trucks placed up wind of the tanks?
- Are the hot oil trucks 100 ft or 50 ft from the tanks? What’s your company’s design spacing requirements for ignition sources / direct fired equipment and oil storage tanks?
- Have you conducted a HAZOP for Hot Oiling Operations? Many accidents happen during non- routine operations.
- Do you have gas detectors? Normally the contractor has a portable. Is that effective? You have RVP issues because it’s winter and cold. Where will the contractor be? In the truck… …where it’s warm.
The hot oil truck is a direct fired (propane) heater with propane storage, and diesel or oil storage. It is normally used to pump hot oil at high pressure down the well’s tubing to melt wax deposits. This operation is normally done for 24 hours/day during winter months to stabilize the crude. It is extremely dangerous, and many flash fires have occurred in the past few years.
These are just some recent examples, but unfortunately there are many, many more…
- August 24, 2018 Fire Crews Battle Tank Battery Fire
- January 25, 2019 Officials identify victims of fire on FM 1788 South
- January 2, 2019 Oil tanks in West Texas catch fire
Heater Treater Fire: https://www.youtube.com/watch?v=XVgg0cZ7H0g
Many Tank Battery Fires are occurring in areas with new unconventional plays like the Bakken and West Texas.
SUMMARY AND CONCLUSIONS:
In this tip of the month, we have identified process safety risks with some designs, solutions to the issues, and evidence that the problem exists.
So my question for you… …after reading this tip, what action do you take to improve the safety of your designs and operations at your company? Your company and colleagues need you to take action.
- Are your designs safe?
- Are your operations safe?
Stay Safe! Let us know if you have any questions.
To learn more about similar cases and how to minimize operational problems, we suggest attending our G4 (Gas Conditioning and Processing), PF3 (Concept Selection and Specification of Production Facilities in Field Development Projects), PF4 (Oil Production and Processing Facilities), PF49 (Troubleshooting Oil & Gas Processing Facilities), and PS4 (Process Safety Engineering) courses.
By: James F Langer, P.E.
References:
- Langer, J.F., Design and Operation of Unconventional Surface Facilities Stabilization Issues, PetroSkills-John M. Campbell Tip of the Month, January 2018.
- “SPE 166261 Distributed-Flux Burners Improve Life of Firetubes and Process Throughput in Heater Treaters”, David Bartz, Michael Silberstein, James Gotterba; ALZETA Corporation, 2013
- “Layer of Protection Analysis-Simplified Process Risk Analysis”, Center for Chemical Process Safety-CCPS, 2001, AIChE, Table 5.2 In-line deflagration arrestor
- API Standard 521, Pressure-relieving and Depressuring Systems. 6th Edition, Jan 2014
Fabulous blog post! Thank you for sharing and Ihave absolutely acquired many ideas.
When is your next blog available?
Good post. Very useful.